When a lot of electro-mechanical systems have been miniaturized and integrated by compact design, thermal management in a small volume should be simultaneously considered. As the devices or systems become smaller, heat flux increases in general. Therefore, an effective cooling strategy for the micro-devices is required especially when the cooling target is made from microfabrication processes. The microfluidic heat exchanger is one of the most promising devices for cooling down the electronic systems because it can be also made by the microfabrication processes1. This device which is also called microchannel heat sink has been considered as an effective heat removal tool and has caught much attention during the past decades, due to its advantages including high heat transfer performance, mild pressure loss and easy fabrication2.
It is evident that the former electronic cooling systems majorly employ heat pipes, fins and a combination of both. The use of the fin and heat pipe based cooling system manages to occupy large volume and appeals a huge setback from the perspective of compactness of the device. For example, a normal heat pipe combined with a fan can dissipate (300W/m2K) energy and at lower magnitude with only fins (80W/m2K)3. But these cannot dissipate the latest range 2000W/cm2K, due to this, the above devices have limitations for recent electronic components. Increasing the surface area and using appropriate liquid coolant is one of the better options to move further. The concept of the microchannel heat sink was first coined by Tuckerman and Pease. His path-breaking work initiated many other researchers to compare their numerical and experimental work with other microfluidic heat exchanger shapes. The geometry of inlet and outlet manifolds which are responsible for distributing and gathering of fluid in channels is an important factor for designing microfluidic heat exchangers. Accordingly, the basic manifold designs are conservative and bifurcation type, as shown in Fig. 1. In a conservative design, there is a single manifold region directly connected to the channels distributing the flow. The dashed line in the manifold shows an alternative for improving flow uniformity and consequently temperature gradient by making the manifold non-uniform or triangular. In bifurcation type, the flow from the inlet is divided into two streams; each is then further subdivided into two more till the number of divisions matches the number of channels4.
Beside this, channels geometry, channels porosity, the fluid type, using ribs in channels and etc. are the parameters which have a significant effect on microfluidic heat exchangers efficiency.
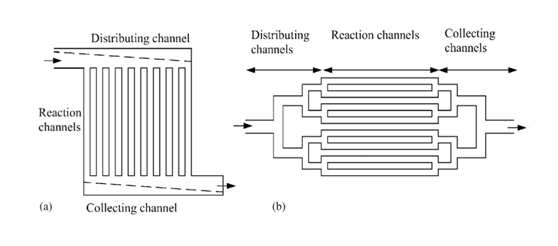
Figure 1. Schematic for (a) conservative and (b) bifurcation type manifold structures4
A heat exchanger is used to transfer the thermal potential of one medium to another, with and without the direct interaction or mixing between them. The ability to transfer heat strongly depends on the contact area between the two medium, a larger area to volume ratio results in more heat transfer. The fluids are typically transferred by a piping network of relatively smaller size, upon entering the heat exchanger it has to be distributed within the heat exchanger so as to increase its contact surface area. Particular care is needed to be focused on this fluid distribution, as the flow rate through each fluid path of the heat exchanger has considerable effects on its performance with regards to pressure drop and heat transfer. The pressure drop in the heat exchanger manifold and channels can be measured experimentally, thus providing the information about the flow distribution characteristics. Such heat exchangers are distinguished by a very high ratio of surface area to volume, low thermal resistances, small volumes, lower total mass, and low inventory of working fluids.
However, it is pertinent to note that the importance of novel technologies in microchannels is not the only hour of demand for high-density electronic components but also to cool data centers, workstation computers, Nozzle cooling for 3D printers, supercapacitors thermal management and cooling of artificial organs. Therefore, the requirement of new sink design to enhance the existing cooling is persuasive by many factors and might provide new insight into many interdisciplinary fields.
Besides the above well-established benefits and application of the microchannel, it has also its own operational limitations as follows5:
- Due to the increased surface area, friction factor increases in microchannels leading to higher pressure drop and it further intensifies while introducing high viscous fluids.
- The use of nanofluids or two-phase fluid develops corrosion in the channels and causes a decrement in heat transfer due to fouling effects.
- The non-uniformity of fluid flow distribution in microchannels leads to the development of hot spots on the electronic device and decreasing its lifespan.
- Identifying an effective manufacturing process for microchannel that provides near zero surface roughness is difficult.
- If point 4 is reality then the concern about early turbulence effects and higher pressure drop can be solved. But, most importantly the primarily responsible factor that influences heat transfer in the microchannel can be cornered.
Multiple interesting microchannel configurations have been proposed in the last decades to fulfill the demands on cooling of the latest electronic devices. Numerous studies are in process for a better understanding of fluid flow characteristic in microchannels and different ways for improvement of efficiency of microfluidic heat exchangers. In the coming years, this device seems to be the most reliable cooling technology due to its superior command overheat carrying capability and it will revolutionize the electronics industry.
1. E. S. Cho, J. W. Choi, J. S. Yoon and M. S. Kim, “Modeling and simulation on the mass flow distribution in microchannel heat sinks with non-uniform heat flux conditions,” International Journal of Heat and Mass Transfer, vol. 53, p. 1341–1348, 2010.
2. Y.-T. Mu, L. Chen, Y.-L. He and W.-Q. Tao, “Numerical study on temperature uniformity in a novel mini-channel heat sink with different flow field configurations,” International Journal of Heat and Mass Transfer, vol. 85, pp. 147-157, 2015.
3. V. R. B. Y. Tullius JF, “A review of cooling in microchannels,” Heat Transfer Eng, vol. 32, no. 8, pp. 527-541, 2011.
4. O. K. Siddiqui and S. M. Zubair, “Efficient energy utilization through proper design of microchannel heat exchanger manifolds: A comprehensive review,” Renewable and Sustainable Energy Reviews, vol. 74, pp. 969-1002, 2017.
5. G. Narendran, N. Gnanasekaran and D. A. Perumal, “A Review on Recent Advances in Microchannel Heat Sink Configurations,” Recent Patents on Mechanical Engineering, vol. 11, 2018.
Enjoyed this article? Don’t forget to share.
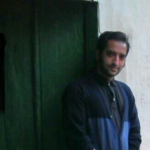
Mohammad Ali Zoljalali
Mohammad Ali Zoljalali is a Master's degree student at the University of Mazandaran. He is working on microfluidics by the focus on microchannels heat sinks and Drug Delivery.